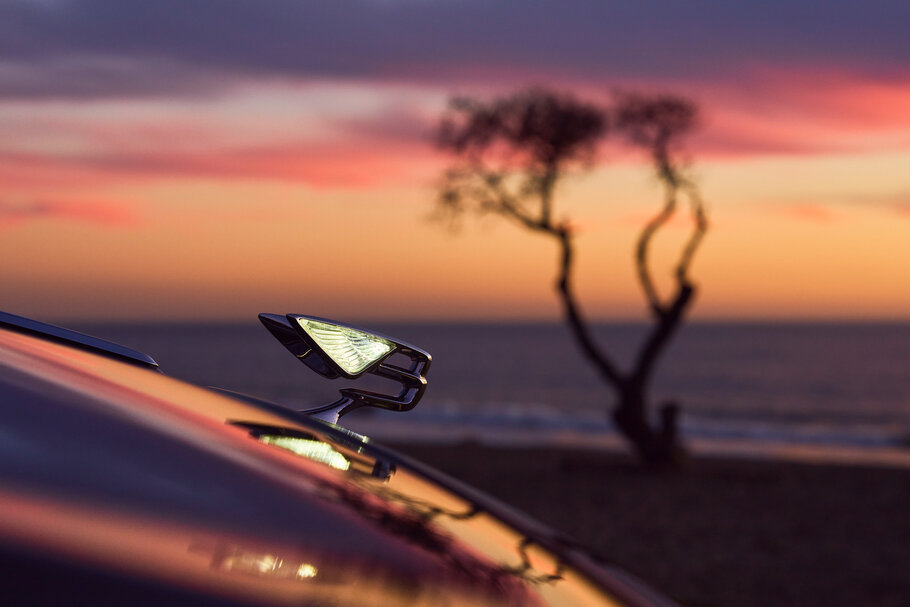
On approaching the Flying Spur Mulliner, owners are treated to a moment of pure automotive theatre. As the Bentley name badge above the grille smoothly slides out of view, a beautifully polished ‘Flying B’ bonnet mascot – the sixth iteration of the design – rises to take its place. In perfect synchronicity, headlamps and the delicate clear acrylic wings of the mascot briefly illuminate with a welcoming glow. Standard of the Flying Spur Mulliner, the ‘Flying B’ is also available as an option on all Flying Spurs – with a 97 per cent uptake.
Creating that moment, and the elegant ‘Flying B’ mascot that draws every eye, called for a fusion of exceptional design, craft and engineering skills. It’s symbolic of Bentley’s approach to creating unique ownership experiences through relentless attention to detail at every stage.
Taking design to the next level
Versions of the Bentley ‘Flying B’ bonnet mascot have been offered since the mid-1920s, with the current design being the sixth iteration. For the latest Flying Spur, Bentley designers and engineers accepted the challenge to take the art and craft of the ‘Flying B’ to the next level. The emblem that graces the radiator of the Flying Spur Mulliner is the first in Bentley history to be deployed electronically, the first to feature a cover plate that replaces it when stowed, the first with clear acrylic wings and the first to be internally illuminated.
During development of the new Flying Spur, a shortlist of candidate designs by the in-house team at Crewe was created in prototype form and presented to the Board for selection. The winning design, by Hoe Young Hwang, was the unanimous choice.
Created using turbine casting techniques
The ‘Flying B’ mascot is cast as a single piece of 316 grade stainless steel, which has an austenitic crystalline structure that’s both very tough and capable of withstanding extremes of temperature. The addition of molybdenum also gives it corrosion resistance, vitally important for a component that’s exposed to the elements all year round anywhere from the arctic circle to the equator.
The ‘Flying B’ is made using the investment (lost wax) casting process, a technique usually reserved for precision components such as gas turbine blades. This form of casting, though time consuming, is typically used for making complex-shaped components that require tighter tolerances, thinner walls and a better surface finish than can be obtained with sand casting.
First, molten wax is injected into a die. A water-soluble core occupies the cavity where the two acrylic crystal wings will sit, while a ceramic central core creates a passage within the wax moulding for the illumination wiring. The wax emblem is then removed from the die and the soluble core dissolved to create a perfect ‘Flying B’ in wax.
Next, the wax emblem is encased in multiple layers of a fine ceramic solution containing colloidal silica and alumina; once these layers have set solid, the wax is melted in a steam pressure chamber to leave a ceramic mould with a hollow cavity in the shape of the emblem.
At this point molten 316 stainless steel, heated to 1,600°C, is poured into the ceramic mould. Once the steel has cooled and set, the ceramic outer skin is removed, while the ceramic core is dissolved under pressure using a caustic solution. The stainless-steel Flying ‘B’ emblem that emerges is then ready for the next stage; shot blasting removes any minute traces of ceramic material and a process called ‘extrude honing’ ensures that the internal passage within is smooth enough for the wiring that will pass through it.
Only after every trace of ceramic material is removed, and the component carefully measured to ensure it meets the precise tolerances required, will the Flying ‘B’ be sent for hand polishing. This final touch of hand craftsmanship brings out the deep lustre of smooth stainless steel.
The entire process takes 11 weeks from start to finish, at which point the mascot is ready for assembly of the crystal acrylic wings, wiring and tiny LEDs that create such a magical effect when deployed.
Evolution of the Flying ‘B’ mascot
The earliest Bentleys were not fitted with a bonnet mascot. The oldest Bentley in existence, EXP2, featured a simple water temperature gauge as a radiator cap directly in the driver’s line of sight. But demand from owners led the company to offer from the mid-1920s an ornate, upright brass ‘B’ featuring wings held horizontally.
During Bentley’s Derby era, (1931-39), artist Charles Sykes was commissioned to create a smaller, more streamlined version. His original design featured a forward-leaning single-wing ‘B’ in the Art Deco style, with facets so that the ‘B’ read correctly when viewed from either side. However, the single wing wasn’t popular with owners and Sykes’ faceted ‘B’ design was altered to feature two rearward-facing wings.
A rearward-leaning Flying ‘B’ was briefly offered for the Derby Bentley MR and MX series overdrive cars, perhaps to signify their sporting character. One disadvantage of this design was that the wings projected back over the bonnet; owners had to twist the mascot sideways when opening the bonnet to avoid denting it!
Iterations of Sykes’ design were offered in modified form for Bentley models up to the 1970s, at which point pedestrian protection legislation banned prominent solid bonnet ornaments and they were discontinued.
In 2006 a revised design of the Flying ‘B’ bonnet mascot was introduced, now with a retractable mechanism, for the Bentley Azure and Brooklands models. Later, the same design was offered as an option for the Bentley Mulsanne. This design retracted upon impact but was otherwise fixed in place; it took until 2019 and the arrival of the new Flying Spur for the Flying ‘B’ to reach its current pinnacle of technical and artistic perfection.