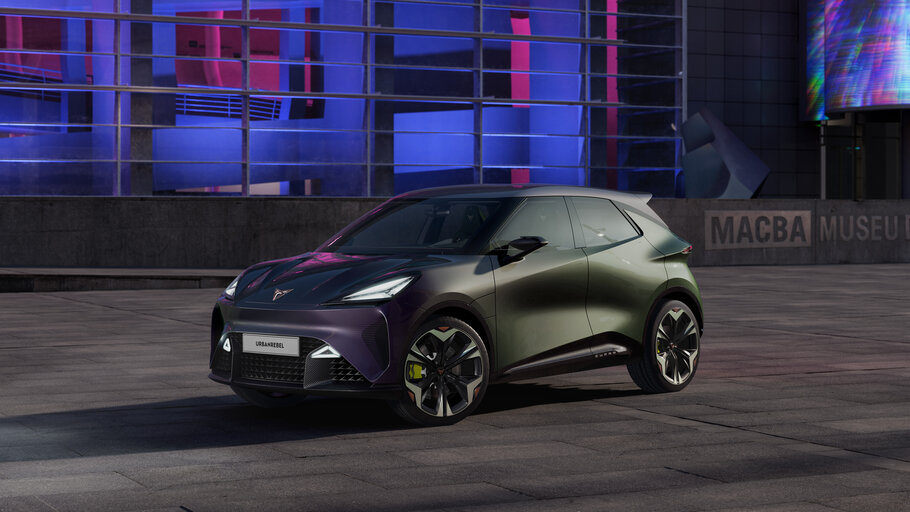
SEAT S.A. will redesign the El Prat de Llobregat plant to be dedicated to electric vehicles with five new projects to produce components for the Small BEV family from 2025.
SEAT Components will produce five components (differential, pivot bearing, battery E-Box, KMM – a battery cooling module – and the aluminium for the motor). This represents a major boost in the repurposing of this centre for the production of electric vehicle components.
With this conversion plan for El Prat, SEAT S.A. is taking another step forward in its ambition to turn Spain into a European hub for electric mobility, and in its own transformation to become a benchmark in the automotive and industrial sectors. To reach this goal the company plans to invest millions of euros in the factory.
Markus Haupt, Vice-President for Production and Logistics at SEAT S.A., said: “The award of new components reaffirms the commitment of SEAT S.A. and the Volkswagen Group to employment stability and the search for alternatives that ensure the future of SEAT Components, as part of the transformation process in which all the Group’s component plants are immersed. The collaboration of the workers and their union representatives is key to the success of this process.”
Currently, around 900 people work in production at SEAT Components. They produce two manual gearboxes, MQ200 and MQ281, for combustion engine cars. The production of electric cars will mean the progressive reduction of these gearboxes and the opportunity to take advantage of its highly skilled workforce and levels of efficiency and productivity. This will drive the development and improvement of new processes to produce components for electric vehicles.
SEAT Components is one of the company’s three production centres, together with Martorell and Barcelona, and one of the Volkswagen Group’s nine dedicated transmission manufacturing facilities worldwide.
Founded in 1979, SEAT Components has been recognised on several occasions for its efficiency and the high quality of its production processes. In 2016, the plant received the Industrial Excellence Award in recognition of its lean management strategy, recognising it as a benchmark in terms of productivity and quality.