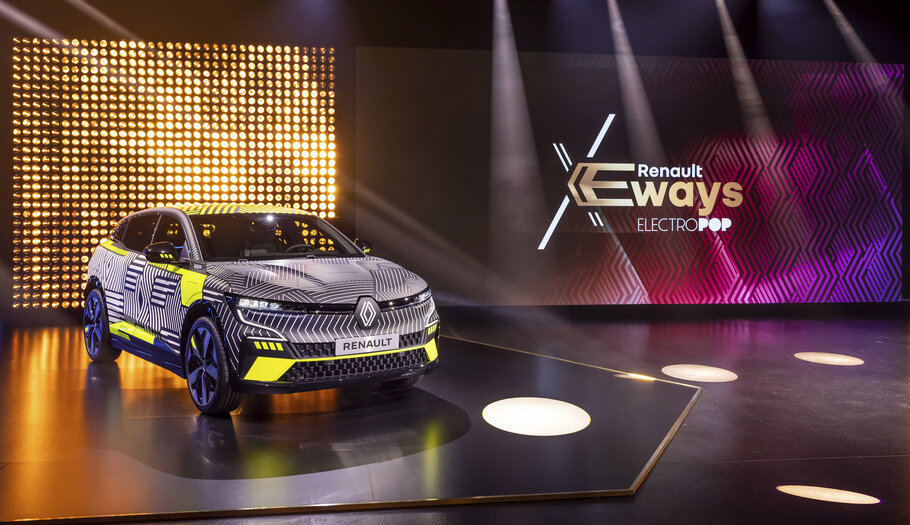
Renault Group has today announced the latest development in its ambition to deliver a broader range of pure-electric vehicles to more potential customers, with an enhanced choice to fit all needs and tastes.
Line-up: Electro-pop cars
The Group will make the best of its dedicated EV platforms, launching 10 new battery-electric vehicles by 2025, seven of them for the Renault brand. The iconic Renault 5 with a modern and electric twist will be made in Northern France, from battery to e-powertrain to assembly, on the brand-new CMF-BEV platform, by Renault ElectriCity.
The Group will also revive another iconic star, currently named 4ever, signifying the intention to make it a timeless classic. Renault Group will also strengthen its presence in the all-electric C-segment, firstly with the All-New MéganE in 2022, while the Alpine “dream garage” unveiled in January will become a reality, starting in 2024.
The Group aims at providing the greenest mix in the European market in 2025, with more than 65 per cent of vehicles in the sales mix electric and electrified, and up to 90 per cent battery electric vehicles in the Renault brand mix in 2030.
“Today is a historic acceleration of Renault Group’s EV strategy, made in Europe. By building our compact, efficient, high-tech electric ecosystem Renault ElectriCity in Northern France together with our e-powertrain MegaFactory in Normandy, we create the conditions of our competitiveness, at home. We’ll train, invest and partner up with established and emerging best-in-class players in their fields: ST Micro-electronics, Whylot, LG Chem, Envision AESC, Verkor. Ten new electric models will be conceived and up to one million electric vehicles will be manufactured by 2030, from cost-efficient urban
vehicles to sportier, higher-end ones. As well as efficiency, we bet on iconic designs such as the beloved R5 to bring the Renault touch to electrification, making electric cars popular”, said Luca de Meo, CEO of Renault Group.
EV-native platforms: delivering high efficiency & optimum range at competitive cost
With CMF-EV and CMF-BEV, the Group capitalises on its 10 years of EV experience making dedicated EV platforms along with its highly efficient CMF-B platform.
For the C- and D-segment, the CMF-EV platform offers enhanced driving pleasure with unparalleled performance. This platform will represent 700,000 units at Alliance level by 2025. CMF-EV offers a range up to 360 miles (580km, WLTP) with very low energy consumption. This performance comes from the Group and Nissan’s engineers working on reduced friction, weight reduction and a state-of-the-art thermal management system.
The architecture pushes the boundaries enabling enhanced practicality with all the technical elements in the engine bay. This architecture removes all crossing cables from the rear to the front and reduces weight and cost. The heating, ventilation and air conditioning system is also located in the engine bay, allowing a narrower dashboard design.
In addition to performance, CMF-EV, which the All-New MéganE will be based on, offers greater driving pleasure thanks to its low centre of gravity and optimal weight distribution, a very low steering ratio allowing quick vehicle responses and a multi-link rear suspension setup.
For the B-segment, CMF-BEV will allow the Renault Group to make affordable BEVs for everyone. At vehicle scale, this brand-new platform will reduce the cost by 33 per cent compared to the current generation Zoe. This has been achieved with the interchangeability of the battery module, a right-sized powertrain of 100kW at lower cost, and all non-EV components caried-over from the CMF-B platform. CMF-BEV will be affordable with impressive performance offering up to 249 miles (400km, WLTP), with no compromise in design, acoustics and driving behaviour. This platform will also feature the Group’s innovative Plug & Charge system that automatically identifies the car, driver and payment based on the NF-C 15118 regulation and secure communication protocol.
Powertrain: from sourcing to manufacturing in-house e-powertrain
By being the first OEM to develop its own e-motor – with no rare-earth (no-permanent magnets) and based on electrically excited synchronous motor (EESM) technology, along with its own reducer – Renault Group keeps one step ahead of the competition. Having already provided most of the investment, the Group has been able to cut the battery cost in half over the past 10 years and will halve it again in the coming decade. The Group will gradually embed new technological improvements from 2024 on its EESM: stator hairpin, glued motor stack, brushless and hollow rotor shafts; lowering costs and improving the efficiency of the motor.
The Group has also signed a partnership with the French start-up Whylot for an innovative automotive axial flux e-motor. This technology will first be applied on hybrid powertrains aiming to reduce costs by five per cent while saving up to 2.5g of CO2 (WLTP) for B- and C-segment passenger cars. Renault Group will be the first OEM to produce axial flux e-motors on a large scale from 2025.
For Power Electronics, the Group will extend its value chain control by integrating the inverter, DC-DC and onboard charger (OBC) into a unique box produced in-house. With a compact design, this one-box project will be 800V compliant, with fewer parts to reduce the cost, and will be used across all platforms and powertrains (BEV, HEV, PHEV). Power modules for inverter, DC-DC and OBC will rely respectively on silicon carbide (SiC) and Gallium Nitride (GaN) thanks to the strategic partnership signed with ST Microelectronics.
On top of these new technologies, the Group is also working on a more compact, all-in-one e-powertrain. This
e-powertrain integrates the e-motor, the reducer and the power electronics (One Box Project) in a single package: enabling 45 per cent less volume in total (equivalent to the volume of the current-generation Clio fuel tank), 30 per cent reduction in cost of the overall powertrain (this value saving being the equivalent of the e-motor cost), and 45 per cent reduction of wasted energy on WLTP allowing an extra EV range of up to 12 miles (20km).
Batteries: mastering NMC chemistry to produce one million units Alliance-wide by 2030
Leveraging its 10-year experience in the electric vehicle value chain, Renault Group’s battery strategy led to bold standardisation choices within the Alliance to offer the greatest competitiveness. With NMC-based chemistry (Nickel, Manganese and Cobalt) and a unique cell footprint, the Group will cover 100 per cent of the future BEV launches across all segments.
It will cover all vehicle types with up to one million electric vehicles Alliance-wide by 2030. This chemistry choice delivers a very competitive ratio of cost per kilometre, with up to 20 per cent more range compared to other chemistry solutions and a much better recycling performance.
The Group will offer two battery types through its partnerships:
- As part of its EV strategy, Renault Group is partnering with Envision AESC which will develop a gigafactory in Douai with a capacity of 9GWh in 2024 aiming to reach 24GWh by 2030. Close to Renault ElectriCity, Renault Group’s partner will produce cost-competitive, low-carbon and safe batteries using the latest technology for electric models, including the future Renault 5.
- Renault Group has also signed a Memorandum of Understanding to become shareholder of the French
start-up Verkor with a stake of more than 20 per cent. The two partners intend to co-develop a high-performance battery suitable for the C-segment of the Renault range (and higher), as well as for Alpine models. The partnership includes the development of a pilot production line for prototype battery cells and modules produced in France from 2022. In a second step starting in 2026, Verkor aims to build the first gigafactory for high performance batteries in France, with an initial capacity of 10GWh, potentially rising to 20GWh by 2030.
In less than 10 years, the Group will drive its costs down step by step by 60 per cent at pack level, with a target below 100 dollars/kWh in 2025, and below 80 dollars/kWh while preparing the arrival of All Solid-State Battery technology within the Alliance in 2030.
Operations: making competitive electric vehicles made in France
On June 9th 2021, the Group announced the creation of Renault ElectriCity to offer “made in France” cars. This new legal entity in northern France gathers the three Renault plants of Douai, Maubeuge and Ruitz, as well as a strong ecosystem of supplier facilities. As soon as 2024, it will be supplied with cost-competitive batteries by the Envision-AESC gigafactory in Douai. It is ideally placed in the heart of the European BEV demand as France, the United Kingdom, Germany, Italy and Spain will represent around two thirds of the total in 2025.
Embodying a successful transition from traditional, internal-combustion engines into electric powertrains, this industrial ecosystem involves the creation of 700 new jobs by the end of 2024. Together with Envision-AESC and Verkor, Renault Group will create 4,500 direct jobs in France by 2030.
The largest production centre dedicated to electric vehicles in Europe, this single entity enables Renault Group to make these plants the most competitive and efficient production unit for electric vehicles in Europe, with 400,000 vehicles produced per year by 2025 and production cost downsized to 3 per cent of the value of the vehicle.
Battery lifecycle: generating additional value throughout the lifecycle
Renault Group is the first carmaker to act on the entire life cycle of the battery. It has developed solid expertise and goes even further with Mobilize to increase their durability, extend their uses and generate additional value at each step of the lifecycle.
- During the first life of the battery in the vehicle, the Group is developing solutions for Vehicle-to-Grid (V2G) that enable energy to be pushed back to the power grid from the battery of an electric car. Of particular interest to grid operators, these power storage solutions can help balance energy load at all times. This way, a car connected for eight hours per day could potentially generate up to 400 euros per year through V2G, allowing EV drivers to offset part of their annual leasing cost, and Renault to capture recurrent profits related to car fleets.
- At the end of their first life in the vehicle, batteries may still contain around two-thirds of their capacity and can be reused for a second life. Mobilize is finding new applications around stationary storage to manage punctual power needs, mobile electricity storage or generators for use in other industries. Renault is pioneering this market and has defined a unique industrial set-up to lead this market in Europe. This is via the collection of end-of-life batteries with the support of its dealer network, the ability to appraise the fair value of batteries thanks to real-time technical monitoring, and the industrial capacity to refurbish batteries at competitive prices and repackage the upcoming 250,000 units of leased Zoe batteries.
Challenging the value chain, the Group plans to collaborate with car rating agencies so that residual value of batteries is taken into account in the used car market transactions for a value up to 500 euros per car. In that view, Mobilize will offer a “health certificate” (for State Of Health monitoring), battery warranty extension contracts, and trade-in offers made possible by the connected vehicle to reassure owners of second-hand electric vehicles.
- End-of-life: Through its subsidiary Indra and longstanding partnership with Veolia, the Group benefits from a robust know-how in EV battery collection and recycling. It has already recycled 75MWh of batteries, half of which were in 2020 alone.
The Group is also deploying facilities for battery retrofitting, re-using, dismantling and recycling through its Re-Factory project in Flins with the objective to generate more than 1 billion euros of turnover from end-of-life and recycling activities by 2030.
Going further in recycling, the consortium recently announced with Solvay and Veolia the recovering of strategic battery materials such as cobalt, nickel and lithium with a very high efficiency and battery-grade quality, so they can be reused in the production of new car batteries.
Evolutions in its battery collection and recycling process will allow Renault Group to divide the net cost of recycling by a third by 2030, while securing an alternative and sustainable sourcing of battery materials at a competitive cost and preserving natural resources.
Previous article
The new Polo GTI: A modern sports car in the best tradition