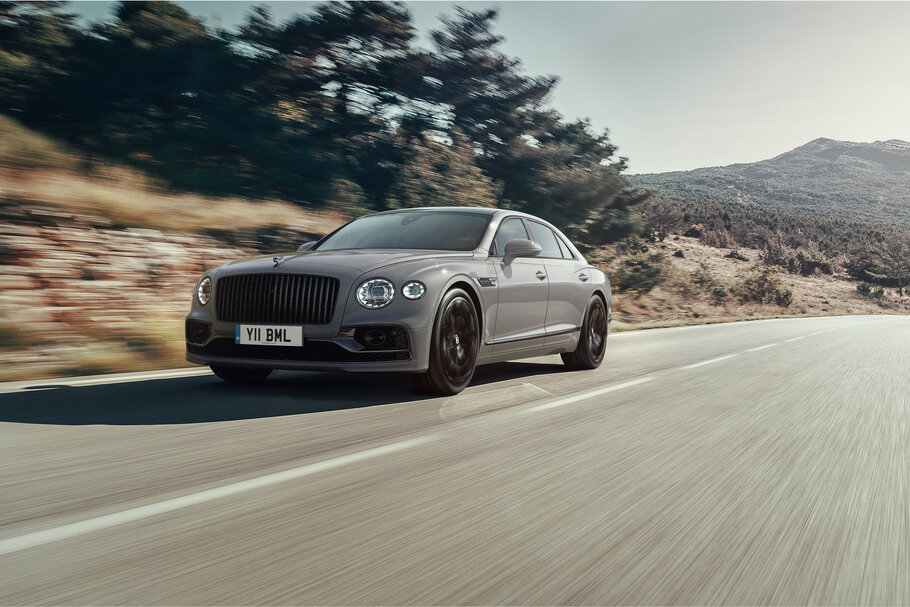
The world’s finest four door sedan has been made even better with increased technology and comfort now as standard, along with new and contemporary interior veneer choices and a new exterior paint – Cambrian Grey, that expands the standard paint palette to 63 colours.
City Specification consolidates an array of optional content and becomes part of the standard vehicle specification at 22 Model Year. These features include; Traffic sign recognition, hands free boot opening, extended safeguard features, top view camera, welcome lighting and automatic dimming mirrors, as well as the Air Ioniser. This adds a greater depth of features to one of the most luxurious cabins of any grand tourer.
The serenely quiet Flying Spur benefits from the application of state-of-the-art technology to deliver the ultimate, in-cabin experience. Noise, vibration and harshness – known in the automotive industry as NVH – have been painstakingly eliminated, helping to ensure the Flying Spur is not only the world’s finest, luxury four-door Grand Tourer, but also offers phenomenal acoustic performance.
The supremely refined and quiet cabin of the Flying Spur, which is designed, engineered and handcrafted in Crewe, continues W.O. Bentley’s aim when he founded the company in 1919. He ultimately met the challenge of building a high-performance luxury car, stating: “I have always wanted to produce a dead silent 100mph car, and now I think that we have done it” when he launched the 8-Litre in 1930. His philosophy of reliability and refinement being the most important features of a Bentley has continued to this day, with the Flying Spur being the epitome of modern Bentley luxury.
Technology and Hand-Craftsmanship
The latest generation of the Flying Spur, offered at 22 Model Year, offers a number of technological benefits for the customer. Traffic sign recognition, hands free boot opening, extended safeguard features, top view camera, welcome lighting and automatic dimming mirrors all become the new standard.
Increasing comfort levels (also as a standard feature), onboard air ionisers emit negatively charged particles from the central air conditioning vents, enhancing cabin air purity and customer wellness. These create a static charge around pollutants such as dust or allergens in the air, which in turn cause them to stick to the nearest surface. The result is to remove such contaminants from the air that the occupants breathe thus improving the feeling of wellness.
Further personalisation is available from now, with the addition of the new Cambrian Grey exterior paint, providing an alternative strong performance look from this technical, solid grey.
In the cabin, new features include the option of open-pore veneer, which is finished with an ultra-thin matt lacquer solely for protection. Liquid Amber, Dark Burr Walnut and Tamo Ash veneers are all available in an open-pore finish.
Selected from only the very best, most figured stock available, open-pore veneer is painted with just three ultra-thin layers of lacquer, together totalling only 0.1 mm in thickness. By comparison, Bentley’s High Gloss lacquer coating is 0.5 mm thick and has a glossy, smooth finish. Each layer is applied by hand and sanded between applications, ensuring the lacquer sticks to the natural grooves of the wood. The resulting finish is wax-like and perfectly highlights the authentic, natural colour and texture of the wood species.
This delicate technique ensures Bentley customers can actually feel the texture of the wood. The variation in colour and grain of different cuts of open-pore veneer mean that each is also slightly different – offering a truly unique Bentley interior.
Luxury Refinement via Digitalisation
To create a cabin environment fit for ‘the best luxury sedan in the world’, one offering unrivalled levels of comfort and refinement, advanced virtual design processes have been utilised in the testing and production cycles of the third generation Flying Spur. These cutting-edge techniques are ultimately more sustainable, dramatically reducing the need to manufacture physical parts.
The challenging job of pinpointing unwanted cabin noise relied on Virtual Prototyping through development partner ESI Group, allowing Flying Spur designers to use digital mock-ups that helped identify NVH before building a physical version of the car. The finely-tuned process enabled acoustic tests for any airborne sounds filtering in to the cabin to be completed, as well as any impact from the structure itself, such as tyre noise.
Through the use of virtual prototyping, a weight optimisation programme for the Flying Spur could be undertaken on 40 different components. This ensured the correct soundproofing materials were deployed in the right locations around the vehicle, so passengers can enjoy the quietest cabin experience possible for work or relaxation on the move.
Sustainability Through Design
The time-saving process also helped engineers keep vehicle weight to a minimum, increasing agility to offer a sublime, driver-focused experience, backed up by a class-leading portfolio of intelligent and intuitive equipment.
Simon Noble, Acoustic Engineer at Bentley Motors, explains:
“By using Virtual Prototyping, Bentley succeeded in what we set out to do –optimise every component of the Flying Spur firstly in the virtual world before we create physical parts. At the same time, we have reduced physical prototypes, creating the quietist in-cabin experience for our customers.
“Virtual Prototyping means fewer prototypes have to be built, and we reduce our testing mileage. It also helps influence the design and engineering of the car at an early stage and affords significant benefits in the extensive testing phase.”
This zero-waste, highly innovative process is also in line with Bentley’s ground-breaking Beyond100 strategy, targeting sustainable global mobility leadership. The company’s ambitious aim is to be end-to-end carbon neutral by 2030, with the Crewe operations climate positive thereafter.
Previous article
New P300 HST broadens Range Rover Evoque line-up