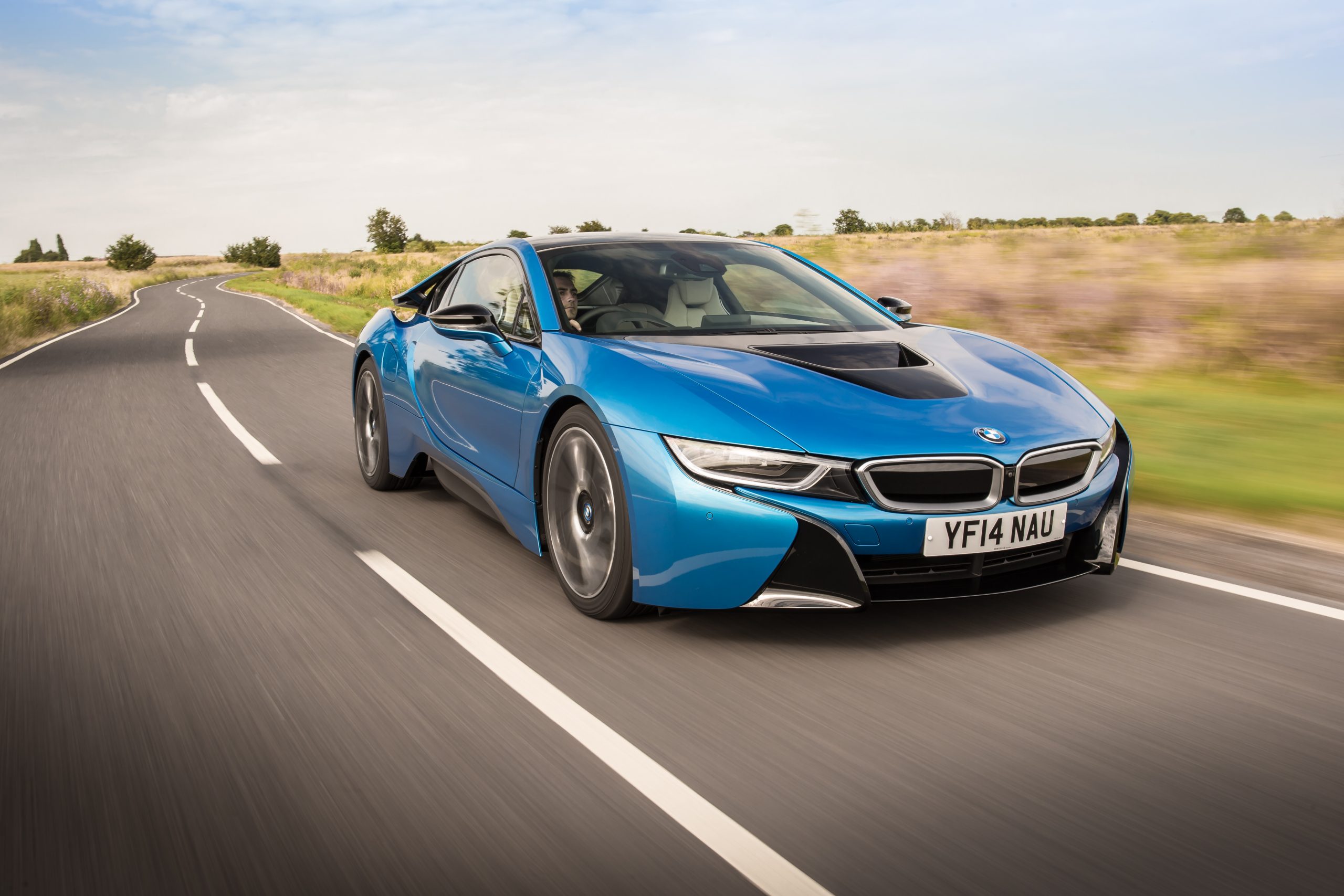
As BMW Group Plant Hams Hall celebrates 20 years of production in the Midlands, we explore twelve pivotal moments and the products that put this North Warwickshire plant on the map as a centre of engine manufacturing excellence.
Today, the latest generation of three and four-cylinder petrol engines roll off the line at more than one per minute, and are supplied to nine different vehicle plants across the world from Oxford, UK, to Germany to the USA. More than five million BMW and MINI cars have been powered by a Hams Hall engine, since the plant first started production in 2001.
Engines aren’t the only thing this plant does well, with key engine components also machined at the site, in a high-tech and complex operation. This area of the business produces more than one million components a year and supplies other BMW Group engine plants in Germany and Austria, as well as Hams Hall engine assembly.
Let’s take a look at the plant’s history and some key moments through a selection of products powered by Hams Hall-built engines.
2001 – 2004: Revolutionary technology launches with the BMW 3 Series Compact.
Production first started at Plant Hams Hall with BMW’s brand-new generation of four-cylinder petrol engines, entering the market with the launch of the BMW 316ti Compact. The naturally aspirated NG4 engine was the first to feature BMW Group’s revolutionary VALVETRONIC technology, which reduced fuel consumption by at least 10%.
It was the first Hams Hall-built power unit to pick up an International Engine of the Year Award. The plant became BMW Group’s ‘centre of competence’ and sole supplier of the four-cylinder petrol engines, between 1.6 and 2.0 litres, that went on to power a number of BMW models.
2005 – 2008: Exports to North America ramped up.
2005 marked a pivotal moment for the plant, as the first engines destined for BMW Group Plant Spartanburg in South Carolina were exported to the United States. These 2.0-litre engines powered the BMW Z4 Coupe.
2006: From the racetrack to the road.
A special production facility was installed at Plant Hams Hall in 2006 to manufacture engines for the homologation of the BMW 320si for the FIA WTCC. In total, 2,600 units of the in-line four-cylinder engine were produced, built by hand on a dedicated production line. The high revving 2.0-litre unit delivered 173hp at 7,000rpm (before reaching its red line at 7,300rpm) and 200Nm of torque at 4,250rpm.
In a direct link with BMW Motorsport’s programmes of the time, before arriving at Hams Hall, the cylinder heads were cast at BMW’s Landshut foundry alongside Formula One engine blocks. The cylinder head cover was made of carbon fibre, reducing weight by approximately 10kg.
From 2006: A new generation of engines for MINI.
In September 2006, the Hams Hall plant expanded its remit with production of an additional, second engine family, supplying the MINI brand and the Oxford production plant for the very first time. An all-new production facility was installed to produce this brand-new engine family, internal code name ‘Prince’, alongside existing NG4 engine production.
This new family of engines – an International Engine of the Year award-winner for eight consecutive years – featured a wealth of innovative technical features which dramatically improved fuel consumption.
A 1.6-litre petrol engine variant powered the new MINI Cooper Hatch to produce 120hp, acceleration from 0-62mph in 9.1 seconds and a top speed of 126mph. Powered by a turbocharged and intercooled version from this engine family, the MINI Cooper S Hatch produced 175hp, covered the 0-62mph sprint in 7.1 seconds and achieved a top speed of 140mph. MINI One Hatch was powered by a 1.4-litre engine derivative with a maximum output of 95hp, that followed in 2007.
From 2010: New and improved engines for the growing MINI family.
Plant Hams Hall powered the ever-growing MINI family, including the all-new MINI Countryman, followed by MINI Roadster and MINI Coupé.
New and improved MINI engines offered more power and torque with reduced emissions and improved fuel consumption. MINI First and One models were fitted with a 1.6 litre engine, replacing the 1.4 litre unit. The iconic Cooper S model was powered by a unit that for the first time, saw the twin-scroll turbocharger and petrol direct injection system offered together with fully variable valve control.
2011: Rear-wheel drive ‘Prince’ engines added to the portfolio.
With the introduction of the new second generation BMW 1 Series in 2011, Plant Hams Hall introduced a longitudinal version of the Prince engine. These units powered a new generation of rear-wheel drive BMW models, including the 114i, 116i and 118i.
2014: Hams Hall became the sole provider of the combustion unit contributing to the electrifying BMW i8 plug-in hybrid sports car.
The purpose-built and technically brilliant BMW i8 plug-in hybrid sports car featured many firsts from the BMW and BMW i brands and the engine was no exception. The BMW i8 Coupé was the first BMW production vehicle to be powered by a three-cylinder petrol engine.
This 1.5 litre three cylinder engine developed 231hp, equating to an exceptional specific power output of 154hp/litre. Combined with BMW eDrive technology together they formed the vehicle’s hybrid system, with a power output of 266kW/362hp achieved and a sprint from 0‒62 mph in just 4.4 seconds.
Both the overall drivetrain and the three-cylinder engine picked up International Engine of the Year awards, including overall winner, best new engine and best in class accolades.
A brand-new and highly flexible production facility was installed for the production of this engine. Hand-built by an experienced and specially trained team, the plant was the only manufacturer of this engine for BMW i8.
2015: A new generation of engines power MINI into the next decade.
Significant investment in the plant came to fruition when a brand-new, high-volume engine production facility started to build BMW Group’s latest generation of three and four-cylinder petrol engines. Plant Oxford was the key customer, with these petrol engines powering the third-generation MINI.
2016: Latest-generation three-cylinder engines for plug-in hybrid models.
Upgraded facilities saw Plant Hams Hall introduce a three-cylinder engine derivative for plug-in hybrids with the BMW 225xe Active Tourer plug-in hybrid the first vehicle to receive this latest-generation engine. The plant continues to produce these engines, and has now integrated production of a four-cylinder derivative. Around a fifth of engines produced at the plant in 2020 were for plug-in hybrid models.
2018: A new high-powered derivative of the four-cylinder Baukasten engine.
BMW Group Plant Hams Hall was the first BMW Group production plant to build a new high-powered derivative of the latest generation four-cylinder Baukasten engine. It was introduced in the BMW X2 M35i, delivering 306hp and setting new benchmarks. The two-litre TwinPower Turbo engine was the very first M Performance series production four-cylinder engine and the most powerful BMW four-cylinder engine ever built.
2019: Supply resumes to BMW Plant Spartanburg.
Another upgrade to assembly facilities enabled Plant Hams Hall to introduce a longitudinal version of the latest generation of four-cylinder engines into production. This engine is supplied for the range of BMW X models and Plant Spartanburg in the USA is the key customer.
2020: Plant Hams Hall builds high-power engines for the MINI John Cooper Works GP.
A rarity with racing genes! Plant Hams Hall built 3,000 power units for the limited edition MINI John Cooper Works GP, the fastest MINI that has ever been approved for road use. A 306hp four-cylinder turbocharged engine accelerates this special two-seater model – based on the MINI 3-door Hatch – from 0-62 mph in just 5.2 seconds.
Plant Hams Hall continues to contribute to BMW Group’s Power of Choice. Production of three and four-cylinder petrol engines, including engines for plug-in hybrid vehicles continues at the Hams Hall plant. Preparations are also underway to take on production of the BMW Group’s prestigious V8 and V12 engine family